Top key factors for choosing the right base metal for custom wire terminal blocks!
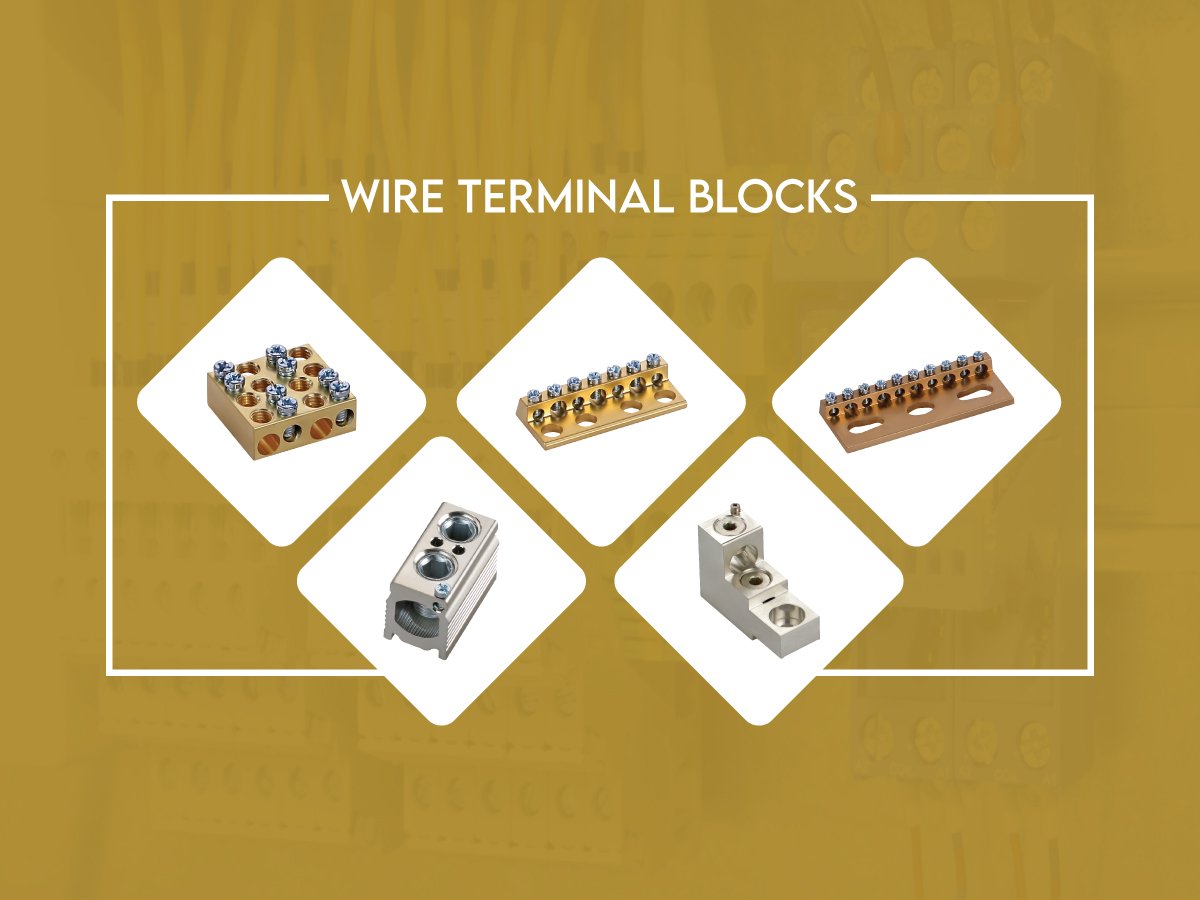
The metal components manufacturing industry uses a variety of materials to create reliable, high-performance products for various applications. But the best suitable metal depends on the specific application and the unique requirements. The leading terminal block manufacturers allow customization of terminal blocks in any type, size, and specification to meet the needs of individuals. From brass, copper, aluminium, to steel, and many other options are available for custom wire terminal block manufacturing. While this broad range of options can make it challenging to choose the right metal material for your custom needs, knowing what factors to consider when browsing the materials available can make the selection process easier.
If you are looking for custom wire terminal block manufacturing services and need help in choosing the right material for your custom wire terminal blocks, the experts at Teron Metal Components have you covered.
Custom wire terminal block designs have many benefits over standard wire terminal blocks. Custom wire terminal block manufacturing allows manufacturers to remove unwanted features, expenses, and complications. Furthermore, they can be made to fit the same application profile as a design specification. But how do we determine which metal is the most suitable for custom wire terminal blocks?
To answer that, in this article, we will look at how different base metals influence the strength, durability, and usability of custom wire terminal blocks. We will outline the most suitable options for high-quality custom wire terminal blocks, so you can make the right decision about whatever base material you choose.
There is a slight difference between material parameters that can make a significant difference to the final performance of wire terminal blocks. Therefore, we will look at the following properties of each metal:
Tensile Strength: Tensile strength tells us the material’s resistance under tension. This is relevant to each metals’ mechanical performance and gives us an indication of the overall durability of the wire terminal blocks.
Types of Metals | Tensile Strength (PSI) | Yield strength (PSI) | Hardness, Brinell (HB) | Density (g/cm³) |
Aluminum – 1050-H14 | 16000 | 14900 | 30 (HB) | 2.7 |
Aluminum – 1060-H14 | 14000 | 13000 | 26 (HB) | 2.7 |
Aluminum – 2024 | 29000 – 79000 | 14000 – 71000 | 47 – 135 (HB) | 2.8 |
Aluminum – 3003 | 16000 – 34000 | 5700 – 30000 | 20-25 (HB) | 2.7 |
Aluminum – 5052-H11 | 28000 | 11000 | 46 (HB) | 2.7 |
Aluminum – 5052-H32 | 33000 | 28000 | 60 (HB) | 2.7 |
Aluminum – 5083 | 41000 – 57000 | 17000 – 50000 | 75 – 110 (HB) | 2.7 |
Aluminum – 6061-T6 | 45000 | 39000 | 93 (HB) | 2.7 |
Aluminum – 6082 | 20000 – 49000 | 12000 – 46000 | 40 – 95 (HB) | 2.7 |
Aluminum – 7075-T6 | 83000 | 73000 | 150 (HB) | 2.8 |
Aluminum – Bronze | 8000 – 147000 | 10000 – 116000 | 40 – 420 (HB) | 7.9 |
Aluminum – MIC-6 | 23900 | 15200 | 65 (HB) | 2.7 |
Aluminum – QC-10 | 72500 – 82900 | 66000 – 76100 | 150 – 170 (HB) | 2.8 |
– | – | – | Hardness, Rockwell (HR) | – |
Brass | 18000 – 150000 | 5000 – 99100 | 54 – 100 (HRC) | 7.2 – 8.6 |
Copper | 32000 | 20000 | 89 (HRC) | 8.9 |
Copper – Beryllium | 70000 – 200000 | 23000 – 180000 | 23 – 43 (HRC) | 8.8 |
Copper – Chrome | 45000 – 77000 | 14000 – 65000 | 65 – 82 (HRC) | 8.9 |
– | – | – | Hardness, Brinell (HB) | – |
Copper – Tungsten | >= 58000 psi | – | 115 – 290 (HB) | 14 – 17 |
Magnesium | 23900 – 29700 | 10000 – 15200 | 30 – 118 (HB) | 1.7 |
Magnesium Alloy | 13100 – 74700 | 3050 – 66700 | 30 – 118 (HB) | 1.3 – 2.4 |
Phosphor Bronze – PB1 | 47000 – 140000 | 19000 – 80100 | 70 – 103 (HB) | 8.9 |
Stainless Steel | 4680 – 450000 | 3630 – 363000 | 80 – 600 (HB) | 0.19 – 9.01 |
Steel – Stainless 303 | 100000 | 62000 | 228 (HB) | 8 |
Steel – Stainless 304 | >= 74700 | 47900 | 123 (HB) | 8 |
Steel – Stainless 316 | 84100 | 42100 | 149 (HB) | 8 |
Steel – Stainless 410 | 221200 | 177700 | 422 (HB) | 7.8 |
Steel – Stainless 431 | 145000 | 89900 | >=248 (HB) | 7.8 |
Steel – Stainless 440 | 254000 | 186000 | 58 (HRC) | 7.8 |
Steel – Stainless 630 | 150000 – 210000 | 130000 – 200000 | 352 (HB) | 7.8 |
Steel 1040 | 89900 | 60200 | 201 (HB) | 7.8 |
Steel 45 | 81900 | 45000 | 163 (HB) | 7.9 |
Steel A36 | 58000 – 79800 | 36300 | 140 (HB) | 7.8 |
Steel Grade 50 | 65300 | 50000 | 135 (HB) | 7.8 |
Steel D2 | 210000 – 250000 | 239000 – 319000 | 55 – 62 (HRC) | 7.7 |
Tin Bronze | 35000 | 24900 | 135 (HB) | 8.7 |
Titanium – Grade 1 | 18000 – 34800 | 24700 – 45000 | 120 (HB) | 4.5 |
Titanium Alloy – Grade 12 | 65300 | 55100 | 180 – 235 (HB) | 4.5 |
Zinc | 5370 – 64000 | 18100 – 56000 | 42 – 119 (HB) | 5.0 – 7.1 |
Conductivity: In the wire terminal block, we need the current to pass across potentially many different interfaces without damaging the electricity. There are many aspects of an electrical device to consider, including strength and machinability. Also, under the remit of conductivity, it is worth considering which type and size of wire terminal blocks you will need.
Metal | Electrical Conductivity (10e^6 siemens/m) | Electrical Resistivity (10e^8 ohms/m) | Thermal Conductivity |
Brass | 15.9 | 6.3 | 150 |
Copper | 58.7 | 1.7 | 386 |
Aluminium | 36.9 | 2.7 | 237 |
Steel | 10.1 | 9.9 | 80 |
Bronze 67Cu33Sn | 7.4 | 13.5 | 85 |
Molybdenum | 18.7 | 5.34 | 138 |
Zinc | 16.6 | 6 | 116 |
Nickel | 14.3 | 7 | 91 |
Carbon steel | 5.9 | 16.9 | 54 |
Stainless steel 316L EN1.4404 | 1.32 | 76 | 15 |
Silver | 62.1 | 1.6 | 420 |
Power: Electrical wire terminal block may require high current and voltage capacity. Based on various industrial applications, some types of wire terminal blocks require a larger contact area. The larger the conductive portion of a connector, the thicker the walls. Though thicker contacts will be more durable, they are usually lower in quality and low in cost.
Cost: It is critical that you choose a material that meets your product’s application requirements and meets the specifications of your production order, all while remaining within your budget.
Metal | Cost |
Brass | Cost-friendly |
Copper | Expensive compared to brass & bronze |
Aluminium | Cost-friendly |
Steel | Expensive |
Stainless Steel | Most expensive |
Bronze | Less expensive to copper |
Application: You should choose the material based on the intended use and application of the wire terminal blocks. Due to its high thermal and electrical conductivity, copper is ideally suited for electrical components that used in electrical and thermal applications, while stainless steel is best suited for components used in food and beverage applications.
Finishes to consider: There are several ways in which materials can be finished to meet functional and aesthetic requirements. As an example, stainless steel is passivated or electropolished, while titanium is anodized or hard coated.
It is important to choose a material that can accommodate a particular metal finish or special coating. You should select a finish that fits your application requirements if you have a specific material in mind.
Adaptability to different forming operations: When selecting a material for metal forming, it is important to consider weldability, machinability, ductility, and formability. These factors are determining how easy or difficult it will be to create the desired custom wire terminal blocks, which can affect project turnaround.
Machinability: This refers to the effort exertion by our tools required to machine a specific material. Machinability is the ability to cut through metal satisfactorily while accounting for cost. For instance, a harder material will take more power, time, and cost to cut through because of the wear exerted on the cutting tools to reach a finished product.
Metals | Machinability Rating |
Free-Cutting Brass | 100 |
Medium Leaded Brass (Alloy C34000) | 66 |
Naval Brass (Alloy C46400) | 50 |
Aluminum Alloy (2011-T3) | 50 |
Leaded Free Machining Steel (12L14) | 21 |
Copper | 110 |
Bronze | 30 |
Steel (Grade 316) | 60 |
Steel (316B) | 50 |
Weldability: There are some metals that are easier to weld than others. If you choose a metal that is difficult to weld, the manufacturing process will take longer and require more expertise. There may be an impact on your budget and timeline also.
Ductility and formability: For custom metal products or wire terminal blocks ductility and formability are also key factors. Metals can take different shapes depending on these traits. A metal with lower ductility cannot easily be shaped into a wire, and a less formable metal cannot be bent without snapping.
You should pick a material with properties that suit the operations needed to manufacture your custom wire terminal blocks.
Need a manufacturing partner for custom wire terminal blocks?
There is no doubt that the metal plays a crucial role in custom wire terminal blocks manufacturing. There are several industries including medical, electrical, electronic, and automobile, where several types of wire terminal blocks are used based on specific requirements. Teron Metal Components is an ISO 9001:2015 certified leading manufacturer and exporter in the field of metal components production and export. We are working with many industries, and providing custom, contract, and OEM manufacturing services for special industrial applications and requirements. Get started with wire terminal blocks or custom metal components. Request a free quick quote today.