Top considerations to select the right material for your custom metal components and parts!
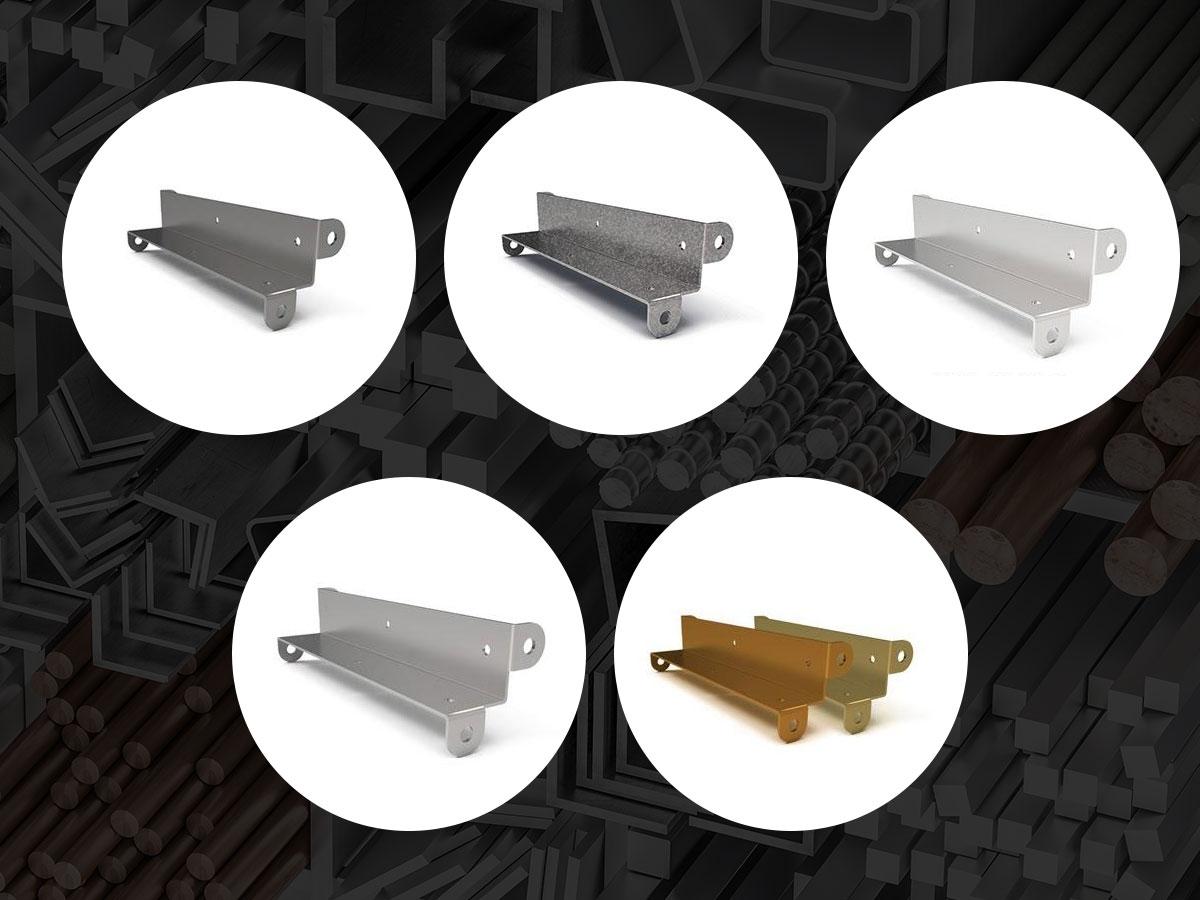
One of the first steps in manufacturing custom metal components or parts is choosing what material you will use. Different materials have different properties, and not all materials are the same or suitable for all applications. Selecting the right metal for custom metal components is critical to ensure proper functionality. The best metal for your metal components will be determined by your customization needs, such as product design, functionality, and the environment in which you will use it. There is an incredible array of metal and alloy options available in the market, selecting the right one from them is not always an easy decision.
In this blog post, we will examine some factors to consider when deciding which metal is the best choice for your custom metal components and parts, so that you can make an informed choice, as you start your next design of custom metal components.
There is top consideration that needs to be evaluated to select the right custom metal components material. Those are:
Metal Strength: A major factor for tension, pressure, and static loads. Materials show different types of strength depending on how the load is applied. These abilities are used as criteria for selecting content for specific applications. The following are the various types of metal strength:
- Yield Strength
- Tensile strength
- Compressive strength
- Impact Strength
Machinability: The ability of a material to be machined is referred to as its machinability. Materials with high mechanical properties can be cut quickly and with minimal effort. Less machined metal may require the use of specialized equipment, which again can affect your costs and time. Some metals are difficult to form or machine, which further complicates the metal components manufacturing process.
Weldability: It is important to choose the metal keeping in mind your welding needs. This is because some metals are easier to weld compared to others. Each metal responds differently to different types of welding methods, some easily malleable metal expands and softens when heated due to welding. When choosing a metal for welding application, there are several considerations. This includes the following:
- Melting Point
- Ductility
- Strength
- Electrical Conductivity
Ductility: The ability of a solid material to deform under tensile stress is referred to as ductility. In practice, a ductile material can be easily stretched into a wire. You need to take into consideration the ductility that determines what shapes a metal can take on. Metals with low ductility cannot be easily shaped. Any metal that is capable of pressing and forming without suffering fractures is considered ductile metal. With a certain amount of heat, all metals are ductile.
Versatility: Is the metal of your choice versatile enough to work with other materials if needed for your project? If not, it may cause problems for your project. If you choose metal for advanced metal components, you must go with a metal that is long-lasting, durable, easy to work with, and versatile. Stainless steel is known for being extremely versatile. Its specific composition can be modified to help make the metal suitable for a particular job in a variety of situations.
Resistance properties: Due to chemical reactions between the metal and its environment, the metals corrode over time. However, some metals are more corrosion resistant compared to others. Corrosion resistance should be a high priority for you if your prototype or custom part is exposed to moisture, acids, salts, or alkalis. Metals with corrosion-resistant properties should also be considered in parts for outdoor use.
As with dealing with all environmental challenges including temperature extremes or high wear, the demands of harsh corrosive environments suggest that metal components manufacturing companies will help select the material that provides the needed performance balanced with a cost-effective solution.
Price: The cost of materials is always the first factor to consider. You can’t choose a metal that goes beyond your budget. If the right material covers all your needs but also increases the budget, then you may need to re-evaluate your design of custom metal components. Depending on the project you should choose pocket-friendly and durable material.
Considering all the factors discussed above will help you make the right decisions and come out with high-quality and precision metal components. And still, if you are not sure how to choose the right metal, or just want to talk about your custom metal component design; then our team of experts at Teron Metal Components can simplify the manufacturing process for you, helping you understand what advantages differentiate each metal material so that you can select the right metal for custom metal components. To learn more about our services and offered range of metal components, contact us by emailing at sales@teronmetalcomponents.com or request a quick quote!