- Home >
- category >
- Metal Components >
Teron Metal Components News & Events
Explore the latest blog and news on metal components, electrical components, earthing components, fasteners, custom manufacturing solutions, industrial solutions, latest industrial trends, and more!
Categories
Archives
Select the metal components exporter that fit your business needs!
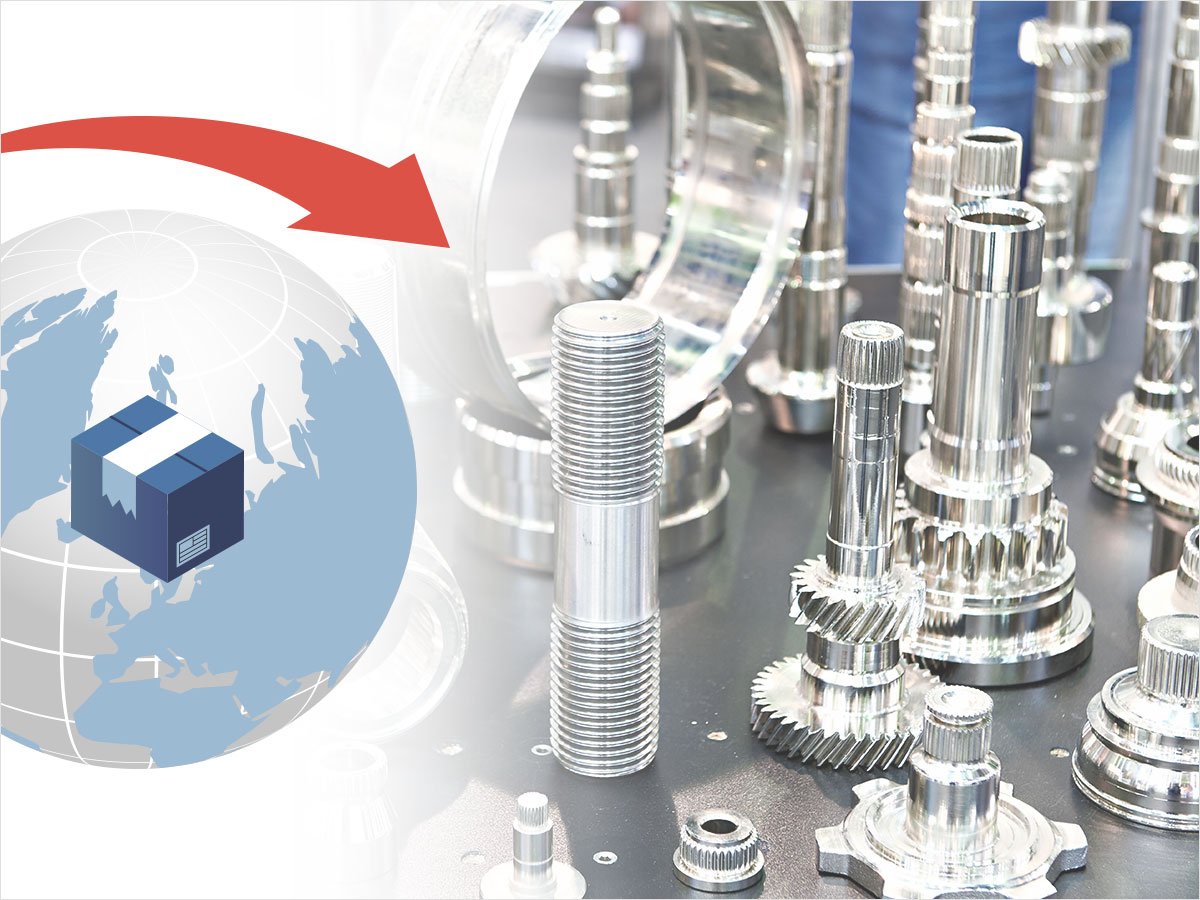
Whether you are tackling a major project or a smaller routine project, it is important to choose the right metal components exporter and manufacturer. In most cases, companies rush into choosing metal components, only to find out they did not get the quality they expected.
Finding the right exporter for metal components and parts can make the difference between being able to work efficiently and dealing with production delays and constant reworks.
The question is, how can you find the right exporter for your business needs?
To help you answer this question, we have assembled a list of several factors you should look at in your metal components exporters to sort out the best from the rest:
Deliver Quality Metal Components
A primary one is the company’s commitment to quality. Take into consideration the quality of the products provided by the manufacturer. It is often the case that quality extends beyond certifications and standards. As an ISO 9001:2015 certified parts manufacturer, we have a definite quality management system to ensure high-quality products. This can encompass a variety of aspects of a company, such as material quality, product quality, service quality, etc.
ISO Industry Certifications
Certifications are another indicator of a quality metal components exporter partner along with their experience. Obtaining a certification indicates that a company is compliant with industry requirements, standards, and restrictions.
It indicates sufficient measures to prevent the production of flawed or faked parts, maintain flexibility in the phase of fluctuating demands, and address safety concerns.
Capabilities and reliability
If you are considering a supplier, ask other customers about their experience with them. Was there an average wait time for orders fulfilled? The supplier might not provide the level of reliability you require if delivery times are long and deadlines are frequently missed. Your metal components partner should be able to meet the parts and production requirements you have, i.e., they should be able to stamp the designs and produce them in the quantities you require according to the specifications and standards.
Responsible and time-oriented
Most companies overlook the delivery aspects when seeking metal components exporter partners. Creating high-quality, cost-effective products that meet clients’ needs is not effective if they cannot be delivered on time. Make sure you choose the right manufacturer and exporter partner who is reliable and can meet your delivery deadlines. Consider the average waiting time for orders to be completed. You should determine if your exporting partner can process the required documentation before delivering parts to the international markets.
Fair cost and value
It is critical to consider the prices that the manufacturer charges for the products. Although a cheaper producer may seem attractive, but you should not take your decision primarily based on price. To achieve the most desirable quality, it is paramount to balance cost and quality. It is also imperative to consider the total cost of ownership, which includes transportation and logistics expenses. Make sure you take time to negotiate the price, do not accept the first quote you receive.
It is essential to find a metal components exporter that meets all your requirements. If you often purchase large volumes of metal components, seek a firm that provides discounted bulk prices.
Invested in Your Long-Term Service
Finally, choose an exporter partner that prioritizes long-term partnerships. It is important to have a strategic business relationship with your metal components exporter. It is important to work with a company that provides you with the support you need to succeed.
Choosing the right metal components exporter means understanding your business needs, being strategic in the procurement of specialty products, and delivering the products on time. Moreover, strategic partners will invest time in strengthening that business relationship and make the investments needed for the continuous improvement of the relationship.
There are many other factors to consider when selecting your exporting and manufacturing partners. At Teron Metal Components, we are an industry-leading manufacturer and exporter of custom metal components and products. As a manufacturer with decades’ worth of experience and a broad range of standard and custom manufacturing capabilities, we manufacture precision, complex, and/or high-performance metal components. We accommodate customer projects involving a variety of metals (e.g., aluminium, brass, copper, nickel, cold rolled steel, etc.) and prototypes to high-volume production quantities.
The most common type of metal surface finishes for the high-quality components!
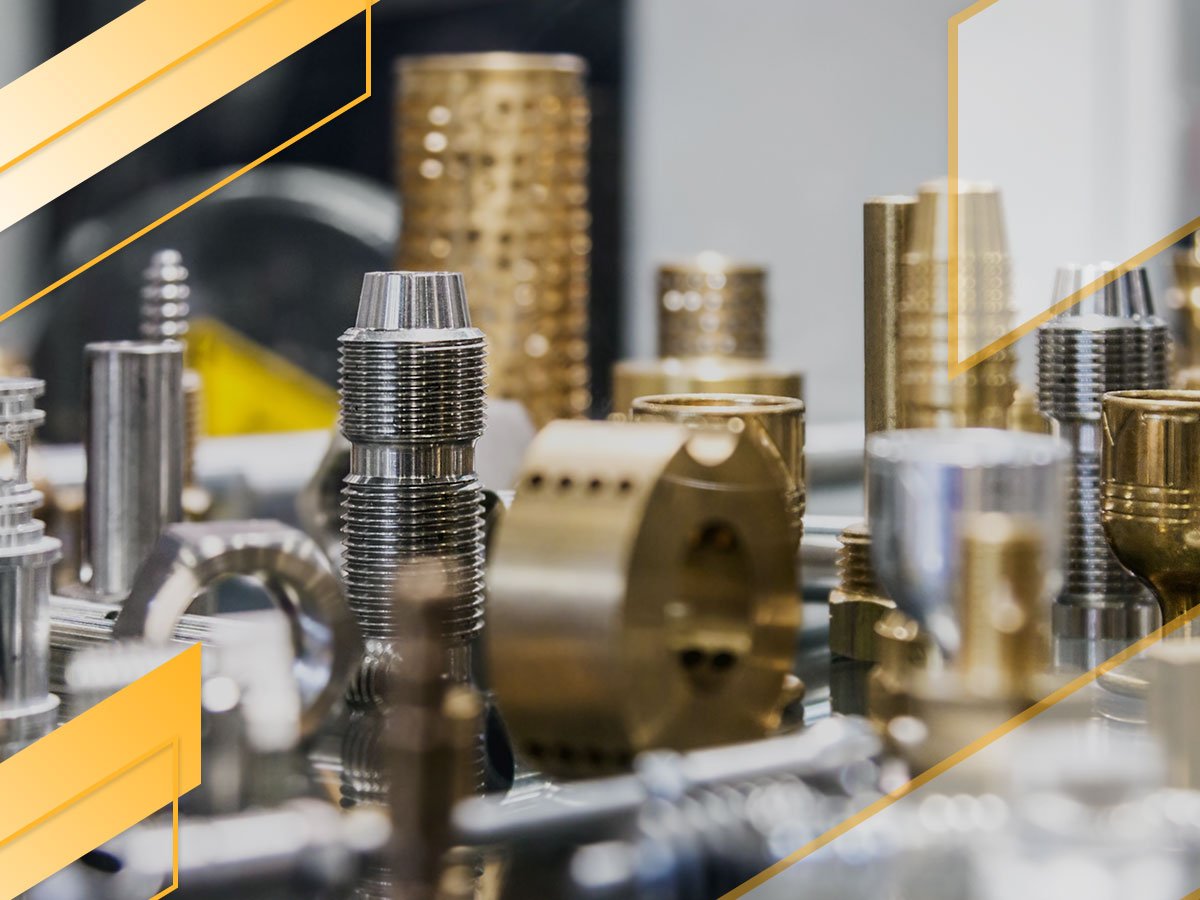
Metal is ubiquitous today, and you can find it anywhere. From little gadgets to huge machinery, furniture, electronics items, and vehicles, everything is the end component of metal.
When you are looking for some quality custom metal components for your project, you must consider all their characteristics, such as their material of construction, performance in various environments, and durability. However, the last two factors depend on the material and the type of surface finishing used. The finishing on the metal components helps improve their performance and lifespan. The surface finishing is primarily for corrosion resistance of metal components and may also be for thread lubrication and, in many instances. There are several types of surface finishing and coating available in the market.
This post discusses several common surface finishings that you can consider while buying metal components for your industrial, commercial, or personal uses.
The Importance of metal surface finishes
Quality is essential for any product selection. When it involves metal parts, products, or components, quality is defined by durability and resilience. Clients want metal products that may last! Because metal components connect or combine elements, structural integrity needs to employ the correct type. Similarly, appropriate surface finishing makes sure the longest lifespan for your metal components by providing a level of protection for the metal underneath.
In addition, damaged or rusted metal parts or products may be dangerous and costly to interchange. Hence, it is crucial that the correct reasonable surface finishing is applied. Manufacturers of metal components depend upon the results of salt spray testing to understand the corrosion resistance of metal components coating. The more hours the salt aerosol container is applied to a coating before oxidation or rust occurs, the higher the coating.
Proving an appropriate surface finish for metal components is a crucial last step in the manufacturing process. It improves the aesthetic appeal of the components and provides extra durability and protection to them. The step is usually used for medical-grade and pharmaceutical components that need to function in clean environments. Different metal components manufacturing companies use different finish options to ensure the beautiful appearance of the parts.
Let’s take a closer look at the most common methods of surface treatment and considerations to ensure the optimum end metal components.
- Anodizing: A finishing process in which a thick oxide layer is added to aluminium to reduce its rust and wear. It protects metal components from the weather and provides electrical insulation at the same time. Various anodizing options are available, including clear anodizing and color anodizing.
- Chromate Surface finishing: It is a chemical treatment that passivates metal to boost its corrosion resistance and electrical conductivity.
- Powder Surface finishing: It includes the application of dry powder (usually made from thermoplastics) electrostatically on the metal components to create a strong finish that makes metals long-lasting.
- Geomet: Geomet is a water-based high-performance thin layer zinc flake anti-corrosion system, which is none embrittling and is available in several grades depending upon the application need. Corrosion performance of the Geomet product range will depend upon specification, surface finishing thickness, surface preparation, and any topcoat applied. All metal components manufacturers worldwide has approved Geomet.
- E-surface finishing: Also, famous as electrophoretic coating, E-surface finishing involves the application of a thin layer of epoxy paint to the metal surface. The surface finishing is applied along with an electric current to make the surface finishing particle deposit perfectly on the metal’s surface.
- Electroless Nickel: Electroless nickel plating is an auto-catalytic reaction used to deposit a surface finish of nickel on a substrate. The solution does not require an electric current to form a deposit, unlike electroplating. As a result of this plating technique, corrosion and wear can be prevented. Compared to electroplating, electroless nickel plating has several advantages.
- Zinc Surface finishing: Many manufacturers of metal components apply zinc surface finishing in two ways – electrolysis or acid zinc. The latter one is metal products but does not always provide a uniform surface finishing, and the former is slower but provides a more uniform surface finishing. The coating prevents corrosion and impacts on metal parts.
- Galvanized Dipped: It involves dipping the metal products into molten zinc to build a strong layer of tightly bonded surface finishing. It prevents metal components from corrosion and is used for automotive and machinery.
- Passivation: By exposing metals like stainless steel to an acid solution, it is possible to extract free iron from their surfaces. Surfaces become more corrosion-resistant when it changes the surface’s reactivity.
- Cadmium: Formerly a popular electroplated or mechanically applied finish, looking like but giving slightly better protection than zinc and providing increased lubricity; also, chromate converted. Due to its toxicity and environmental unacceptability, it is rarely used today. Most often, it is specified through habit, error, or ignorance, and it may be confused with zinc if it is specified.
- Gray Phosphate: This is another important surface finish that is designed to improve the lifespan of metal components. However, this type of surface finishing is not recommended for conditions where there is an elevated risk of corrosion.
- Ceramic Coated: Ceramic surface finishings are not as resistant to corrosion as stainless steel, but they are often used in marine applications as they do provide protection against saltwater spray. These surface finishings are often designed to pass 500- and 1,000- hour salt spray tests.
- Hot Dip Galvanizing: Hot dip galvanizing will allow much heavier surface finishings, the normal commercial surface finishing is approximately 50 microns (µm), which necessitates the over-tapping of the mating thread, and metal components should be as strong as possible to avoid serious compromises in strength. As opposed to electroplating, the deposits are concentrated at the thread roots and corners.
- Dacromet: The finishing process combines zinc and aluminium flakes with a binder for cold-dipped or sprays applications.
Still unsure what metal components surface finishing to use?
Each of the surface finish of metal components listed above is designed to improve overall performance and protection. Although, determining which surface finishing is best depends on its application and corrosion resistance level. Selecting the wrong surface finishing can negatively affect the performance of your metal components, so get in touch with an industry expert like Teron Metal Components. Our experienced team is always ready to help you select the right materials for your next metal components project. Contact us today!
Corrosion Resistant Metal Components: The causes of corrosion and prevention tips.
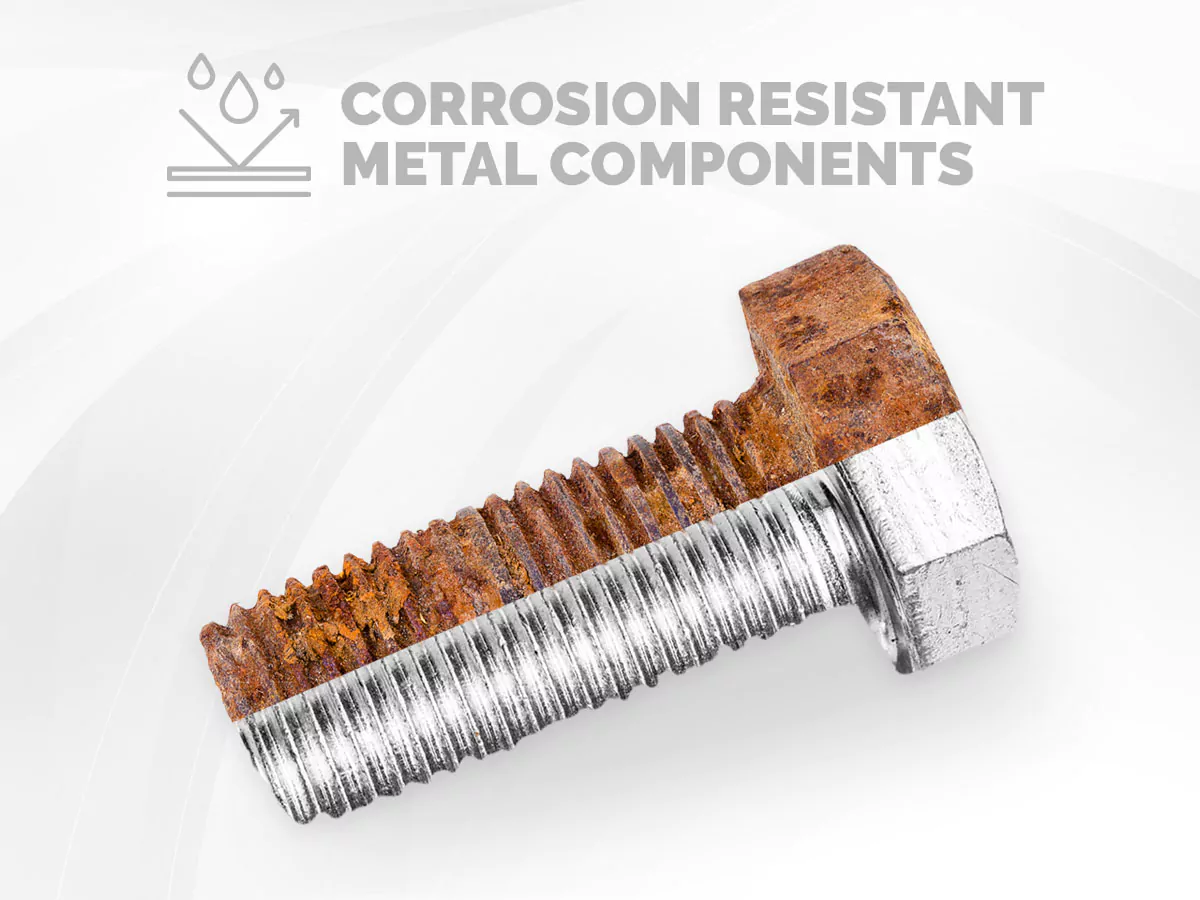
There is no metal that is completely corrosion-proof. It is possible to stop corrosion before it creates a problem by slowing, managing, or stopping it.
During the design process, engineers can consider corrosion control. In order to protect metal components from corrosion, manufacturers can apply corrosion barriers. Finally, people who use the component can take preventative measures to extend its lifespan.
Let’s first know about corrosion.
What is Corrosion?
When metals react with oxidizing agents in their environment, corrosion occurs. In the long run, this chemical reaction can cause the metal to degrade, tarnishing its appearance and compromising its structure.
It is important to note that each type of metal has different electrochemical properties. Depending on these properties, the part will be vulnerable to different types of corrosion. As an example, iron tools rust after being exposed to moisture for a long time, while copper roofs tarnish with time. No metal is immune to corrosion (depending on the environment), but some metals can withstand some corrosion better than others.
Metal components cannot be prevented from corrosion with a one-size-fits-all approach. In order to prevent and control corrosion in different metals, metal components manufacturers must use a variety of methods.
How does Corrosion happen?
If you want to keep your metal components free from corrosion, it is important to know and understand what exactly causes corrosion. With the knowledge of the causes of corrosion, you will be able to effectively prevent it from consuming your metal objects: from heavy machinery to little metal tools.
Metal corrodes when moisture, metal, and an electron acceptor, such as oxygen, are present. Iron is quickly oxidized by moisture when it comes into contact with it, resulting in iron oxide (rust’s chemical name). Although iron corrodes faster than most metals due to its high reactivity, all metals are susceptible to oxidation.
A small amount of corrosion can quickly become a big problem. Your business can lose thousands of dollars when it destroys the functionality and stability of machinery. It is essential to know how to prevent rust effectively to save money and avoid serious problems later on. Taking small precautions upfront can save you a lot of money, time, and frustration down the road.
Let’s explore several considerations that can help keep your beloved metal components from corroding:
How do protect metal components from Corroding?
- Metal Material: Selecting the right material for your metal components is very essential. Metals such as stainless steel are commonly used to prevent rust or to slow it down. Metals such as aluminium are corrosion-resistant, which makes them ideal for use in marine, urban and industrial environments.
- Oiling and Greasing: Rust can be prevented or slowed down by coating metal with oil, which prevents moisture from reaching the iron. The issue of an oily surface may be a problem for some tools or machines as well as a health and environmental concern.
- Barrier Coatings: Special rust preventative products dry with no residue and form a protective barrier over metal components and equipment. They can be used for products in use, shipping, storage, and more. It is important to paint metal to prevent moisture from reaching it in order to slow down rusting.
- Protective storage: Coatings can provide a level of protection against corrosion by acting as a physical barrier between metal parts and oxidizing elements in the environment. It is also possible to prevent corrosion of metal components by powder coating. By properly applying a powder coating, the surface can be sealed from the environment, preventing corrosion.
- Electric Protection: An electrical current is used to overpower corrosive current in a part, using an outside electrical current. Anodes used as sacrificial anodes are less complicated ways to prevent cathodic corrosion. Using a small, reactive metal, you attach it to the part you want to protect.
- Preventive Maintenance: It prevents your metal components and machinery from corroding in the first place. It takes a lot of time to maintain your home, and everyone seems to be short on time. However, maintenance and monitoring are essential to the success of these measures.
- Manufacturing Design: When you are going with the manufacture of custom metal components, the process and manufacturing parameters need to be considered for the selection of the right material; drainage geometry; Electrolysis of dissimilar metals; sealing crevices; corrosion allowance; and maintenance and inspection requirements.
- Chemical Inhibitors: Corrosion inhibitors reduce corrosion rates by slowing down the chemical reaction (corrosion). Generally, corrosion inhibitors are applied to clean surfaces and allowed to penetrate and dry.
- Corrosion management: To prevent corrosion and reduce its costs, a proactive corrosion management plan must be implemented to improve the design, operation, and maintenance of critical assets. Furthermore, these plans should be based on changes in how corrosion decisions are made within an organization.
- Environmental Control: The environment plays a significant role in the likelihood of corrosion. By keeping metal parts and components dry and clean when not in use, you extend their life. You may want to consider methods for controlling the level of oxygen, sulphur, and chloride in the environment if you plan to store them for long periods of time.
Keep your metal components corrosion-free by keeping them safe from the causes of corrosion mentioned above. Careful material selection mitigates the risk of corrosion. Dissimilar material combinations should be avoided when selecting metal for underwater and hazardous environmental applications. Always check the metal components manufacturer’s guidelines before doing so.
We at Teron Metal Components want your equipment to last as long as possible, and we have a wide selection of excellent metals to choose from, such as our mild steel, stainless steel, aluminium, tool steel, alloy steel, brass, bronze, copper, and more. We’ll be glad to help you find the right materials for whatever type of metal components you want to start.
For more information about our Metal Components and capabilities, please contact us or request a quote.
Why should you prefer custom metal components manufacturing?
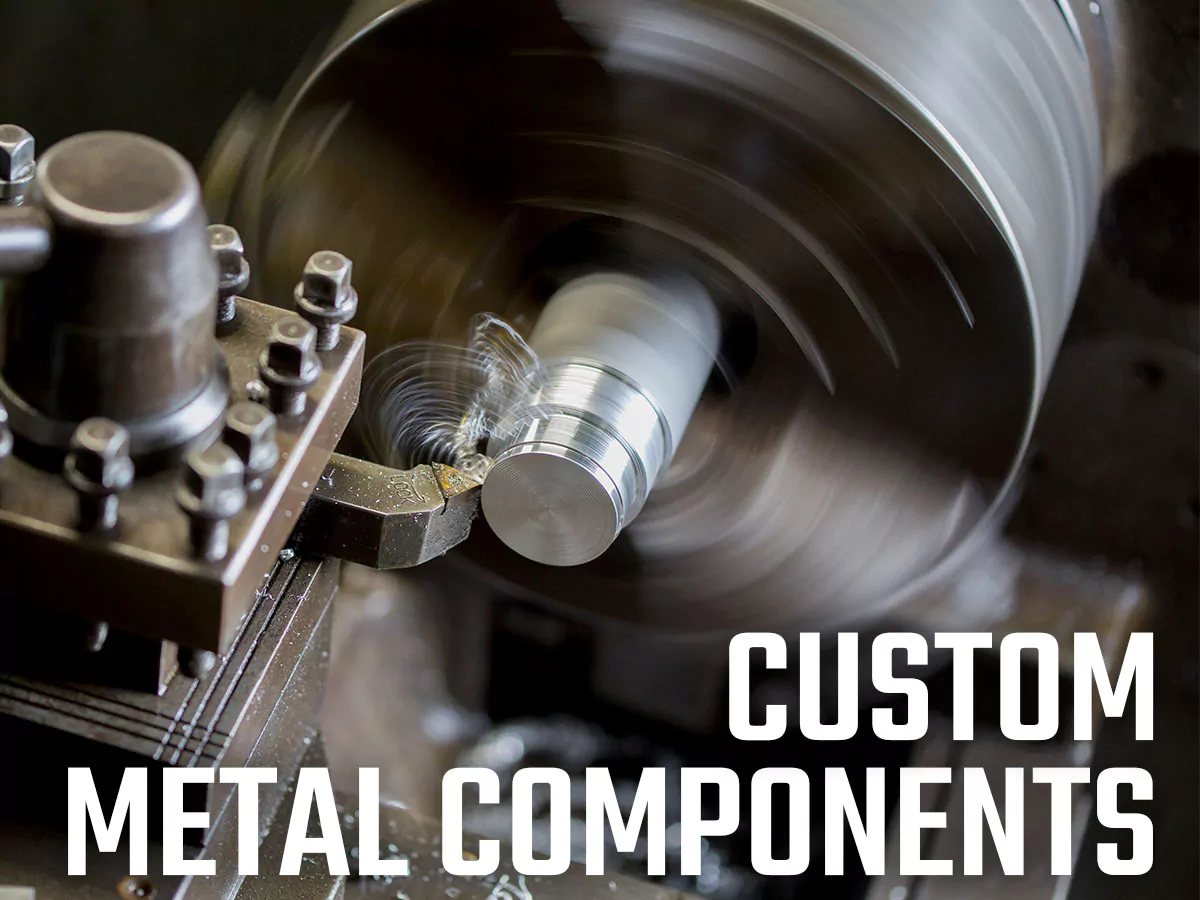
If your business needs metal components or metal parts, there are three options for you: bulk manufacturing, in-house manufacturing, and custom manufacturing. While all have their own pros and cons, we believe that custom manufacturing is more reliable and beneficial compared to any other method.
What is Custom Manufacturing?
Custom manufacturing refers to the customizable application of different manufacturing processes to manufacture parts or products. The custom manufacturing process, as opposed to traditional manufacturing, allows for application-specific product manufacturing. Depending on the application requirements, product specifications and configurations may vary across industries. Custom manufacturing provides complete flexibility in production to meet the needs of various industries. This approach is not limited only to designing and manufacturing custom products, but also to ensuring their long-term quality and performance.
Why should you opt for custom manufacturing?
The metal Components manufacturing process involves several processes such as casting, molding, cutting, drawing, folding, forging, shaping, machining, rolling, punching, shearing, rolling, etc. However, not all of these procedures are required to manufacture certain metal components or parts. The ones that are necessary will vary depending on application requirements. This is where custom manufacturing can help. It enables metal components manufacturers to choose the best manufacturing process for the precision custom metal components. Let’s take a look at some of the key advantages of using custom manufacturing to get the right metal components:
Components with high compatibility:
The customization of metal components manufacturing offers component compatibility. Because all metal components are designed and manufactured based on specific dimensions and specifications, they are usually compatible with one another.Lifecycle of metal components
Custom manufacturing helps to manufacture durable metal components. Based on customer-specific requirements, the manufacturer can select the best suitable that is highly compatible with the desired application. The manufacturer can consider the manufacturing process as well as the chemical reactions that occur during the process. As a result, this creates highly durable and reliable custom metal components.Increase productivity
Custom metal components can be manufactured in a variety of ways by combining multiple processes. Custom manufacturing allows for the selection of the optimum manufacturing process that perfectly suits requirements and helps accelerate product efficiency. In custom manufacturing, the manufacturer can eliminate such processes that affect productivity such as friction, component overlapping, and others. Custom metal components can be made more efficient by streamlining these processes.Cost effective
In most industries, buying a custom metal component means paying slightly more than buying something bulk manufacturing. However, custom manufacturing can actually save money in the long run. Buying custom metal components from a third party is far less expensive than hiring the right custom metal components, manufacturer, and exporter.Improving manufacturing quality
Custom manufacturing allows you to work with an experienced and expert team that helps to provide you with precision and quality custom metal components. Based on requirements, manufacturers work with a state-of-art manufacturing process that can reduce production error and imperfection. A manufacturer must ensure the proper operation of their own machinery through regular inspections and maintenance in order to provide quality metal components.Scalable
Bulk manufacturing incentivizes businesses to buy in bulk. If you don’t require as much, that can create a huge roadblock. Instead of ordering more than you need, the right custom metal component manufacturer can provide you with the exact amount of product you require. When it comes to scaling up, custom manufacturing is also beneficial. Custom manufacturers can handle larger orders if you need a large quantity of a product, or a new product takes off.
Those are some of the key factors to select custom manufacturing over traditional manufacturing or bulk manufacturing. Bring this multitude of benefits to your business with the expert manufacturing team at Teron Metal Components.
The qualification, experience, and excellence of the manufacturer make a huge difference in the final product. This process involves accurate designs, and manufacturing practice.
Therefore, one should always go for a prominent custom metal components manufacturing service provider like Teron Metal Components. The company has been providing manufacturing services for light to heavy-duty metal components and parts for 31+ years. By choosing us as a custom manufacturer, you get to support a global business that works hard to produce high-quality metal components and offer exceptional customer service.